Lifelong
Download Pdf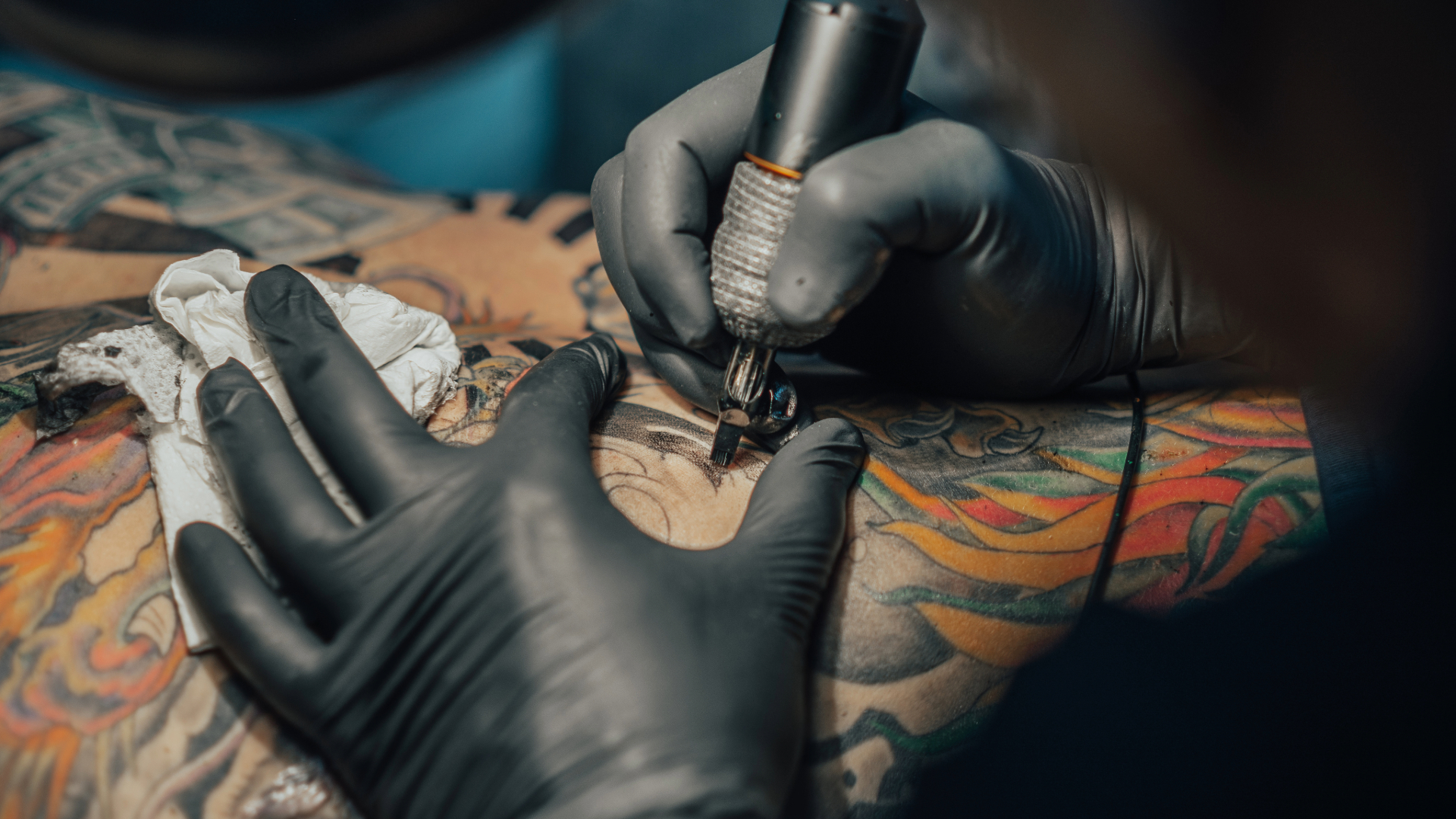
During tattooing, the needle deposits ink into the dermis, beneath the epidermis. This process is repeated numerous times per minute. The quality of the tattoo is determined by the materials employed. High-quality materials are essential for a visually appealing, safe, and comfortable tattooing experience for the artist.
Tattoo needles are in direct contact with skin, ink and body fluids. To avoid the possible release of contaminating particles, the use of stainless steels such as AISI 316L is recommended. Structurally, the hardness of stainless steel prevents deformation during use, allowing the needles to maintain their shape and to ensure the precision of each stroke. This results in defined lines, homogeneous shading and less effort for the tattooist.
The needle configurations require stainless steel to maintain their shape and function during long tattooing sessions. There are different types:
- Round Liner (RL): needles grouped in a compact circular pattern. They are used for precise outlining, achieving defined and consistent lines.
- Round Shader (RS): the arrangement is similar to the RL, but with a more open pattern. Indicated for soft shading and filling in smaller areas.
- Flat: these needles are aligned in a straight line. Suitable for broad, uniform strokes, as well as creating shading effects.
- Magnum: these are arranged in two lines of stepped needles. They are used to cover large areas with soft shading and gradients.
- Curved Magnum (CM): similar to Magnum but with a slight curve at the ends. They fit the skin better, achieving more natural transitions in curved areas.
Electropolishing as an added value
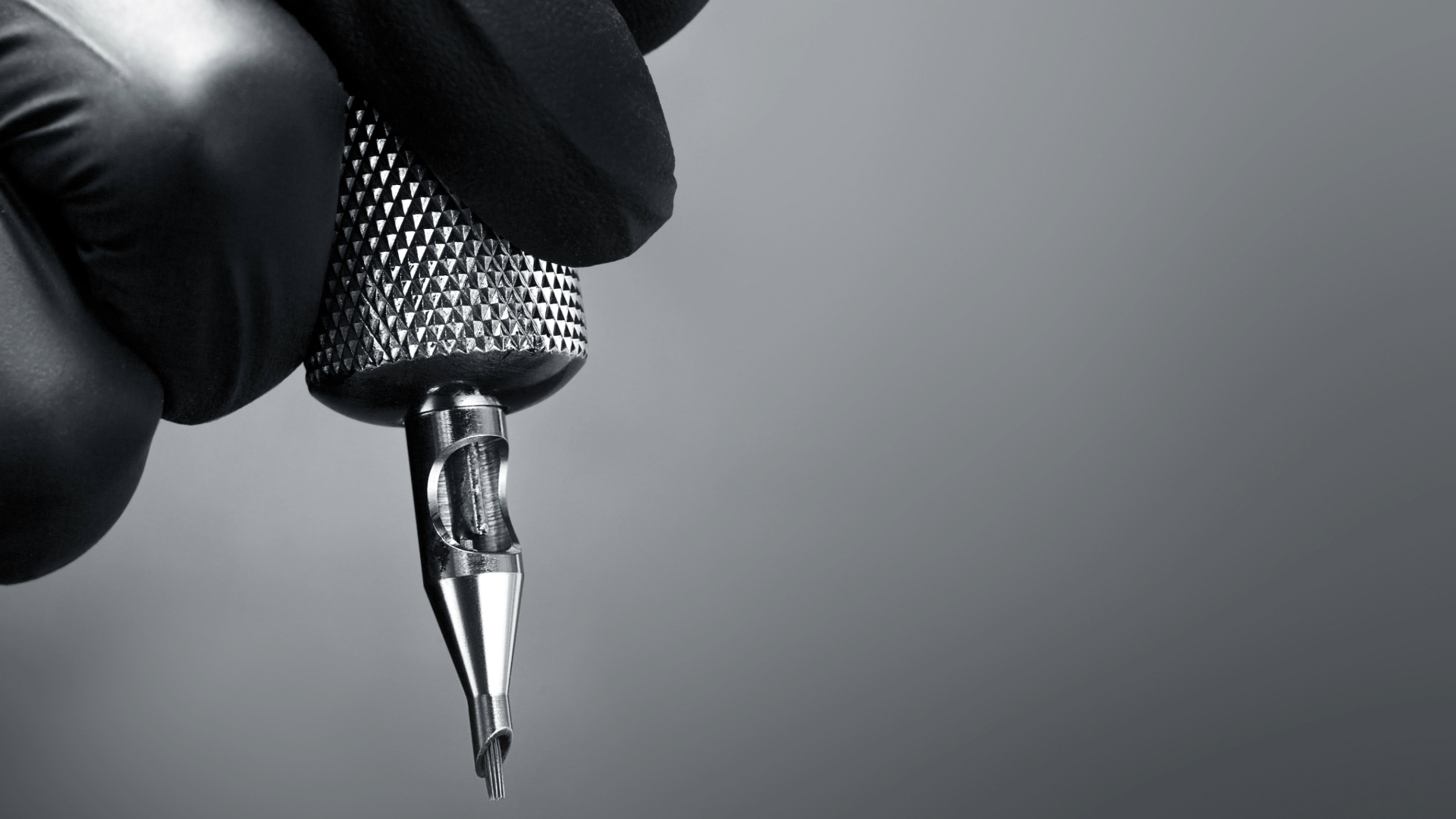
Some needles are electropolished, an electrochemical treatment that improves their surface finish.
When we look at the surface of a metal at a microscopic level, it can have irregularities, small roughnesses. Electropolishing acts to smooth that surface, reducing the micro-roughness. By eliminating microscopic irregularities, friction with the skin is reduced and the precision of the needle on the tattooing process is greater, which reduces skin trauma and promotes healing. We also have to take into account that a smoother surface reduces the risk of dirt or residue adhesion, improving the cleanliness of the surface.
Electropolishing is a beneficial treatment in the manufacture of tattoo needles, as well as for other applications with high demands on corrosion resistance and cleanliness, such as the pharmaceutical, biochemical and food industries. Because electropolishing does not involve mechanical, thermal or chemical impact, items of almost any shape, size and mechanical brittleness can be subjected to this process.